Concrete Batching Plant: Essential for Modern Construction
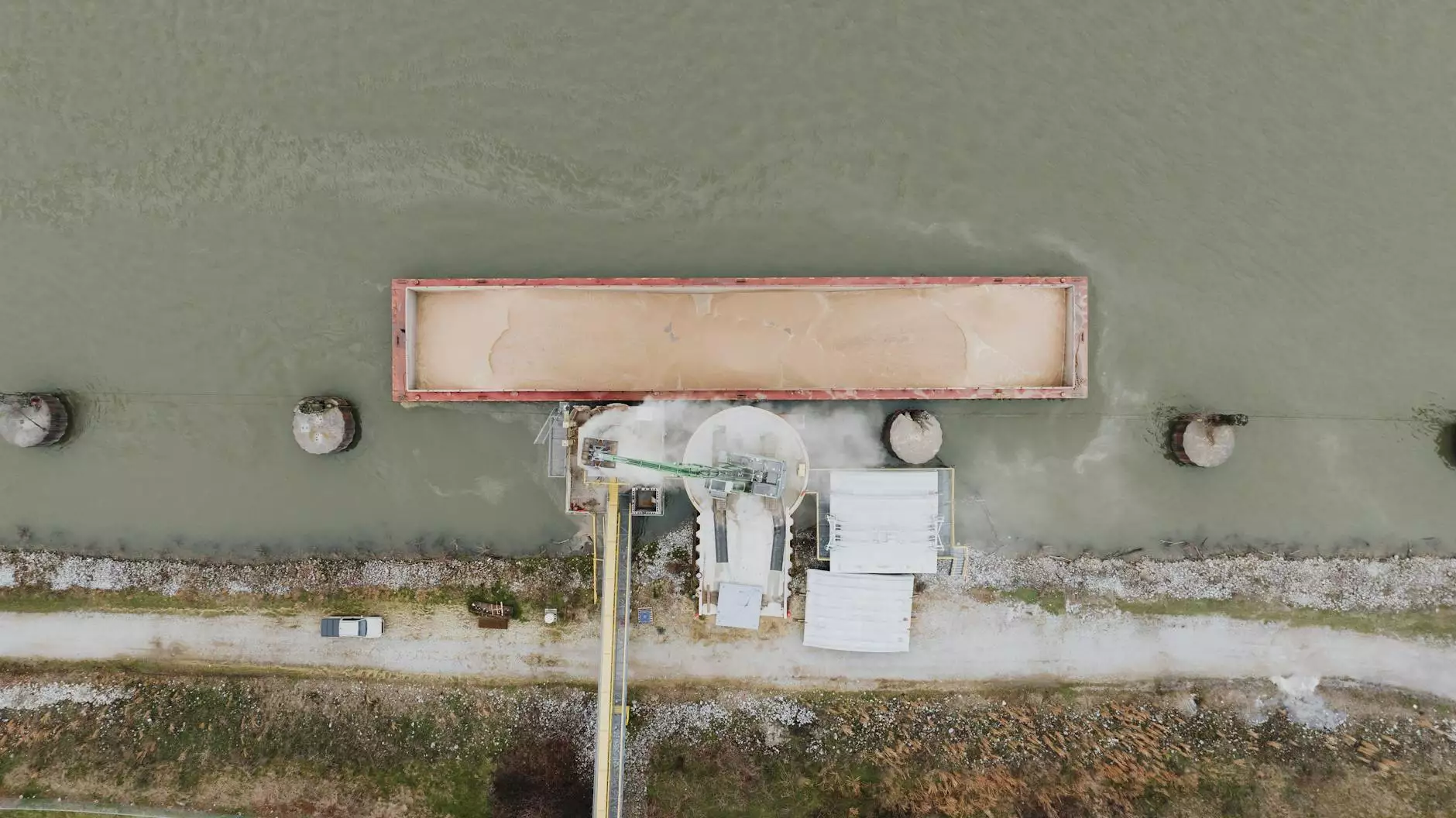
In the fast-paced world of construction, efficiency and precision are paramount. The concrete batching plant stands at the forefront of this industry, delivering precisely mixed concrete for various applications. As the demand for quality construction increases, understanding the intricacies and advantages of concrete batching plants has never been more crucial.
What is a Concrete Batching Plant?
A concrete batching plant is a facility that combines ingredients to produce concrete. The main components of a batching plant include:
- Cement Silos - Store cement, which is a primary ingredient in concrete.
- Aggregate Bins - Store different sizes of aggregates (gravel, sand, crushed stone).
- Mixers - Combine cement, aggregates, water, and additives to produce concrete.
- Control System - Automates the batching and mixing process for consistent quality.
Types of Concrete Batching Plants
Concrete batching plants can be classified into two main types based on their structure and operation:
1. Stationary Concrete Batching Plant
Stationary plants are fixed installations that provide high-capacity output. They are ideal for large-scale projects due to their robust and durable design. These facilities often consist of:
- High-capacity mixers for producing vast amounts of concrete quickly and efficiently.
- Multiple aggregate bins for handling various types of materials, ensuring flexibility in concrete production.
- Advanced control systems to guarantee precision in mixing ratios.
2. Mobile Concrete Batching Plant
Mobile batching plants are portable and can be easily relocated to various job sites. They offer the advantage of quick setup and can be customized based on specific project needs. Key features include:
- Compact design makes transport and installation effortless.
- Flexibility in volume and material requirements enhances productivity on-site.
- Built-in mixers facilitate immediate production and use of concrete without lengthy delays.
Benefits of Using a Concrete Batching Plant
Investing in a concrete batching plant yields numerous advantages. Here are the key benefits that make them indispensable in construction:
1. Quality Control
With a batching plant, producers can ensure that every batch of concrete meets industry standards. The automated process minimizes human error and upholds consistency in quality.
2. Cost Efficiency
Though initial investment costs might seem high, a concrete batching plant significantly reduces operational costs over time. By minimizing waste, optimizing resources, and speeding up the mixing process, businesses can increase profitability.
3. Flexibility in Production
Concrete batching plants can adjust their outputs to meet varying demands and specifications. Whether it's high-strength concrete for infrastructure projects or more conventional mixes for residential buildings, batching systems can be tailored to provide exactly what is needed.
4. Enhanced Logistics
By being located closer to job sites, batching plants reduce transportation time and associated costs. This strategic positioning allows for faster delivery and a more organized workflow, essential in keeping up with construction schedules.
5. Environmental Benefits
Modern concrete batching plants are designed with sustainability in mind. Many facilities incorporate recycling systems to reclaim aggregates and reduce waste. This not only benefits the environment but also contributes to cost savings.
Key Components of a Concrete Batching Plant
The efficiency of a concrete batching plant hinges on its components. Here’s a closer look at each element and its significance:
1. Aggregates Storage
Proper storage of aggregates is essential for maintaining material quality. Effective storage systems prevent contamination and ensure the right proportions are always available for batching.
2. Water Supply System
Water is a critical ingredient in concrete production. A well-designed water supply system should include features to measure and control water flow accurately, contributing to the desired concrete consistency.
3. Cement Feeding System
This system is responsible for transporting cement from silos to the mixer. Efficiency and speed in this process are vital for maintaining production flow and minimizing downtime.
4. Control System
Modern batching plants utilize advanced control systems that enable operators to monitor and manage the mixing process remotely. This not only enhances precision but also improves safety and reduces labor costs.
Integration of New Technologies in Concrete Batching Plants
The concrete industry is continuously evolving, and technological advancements play a significant role in improving batching plant efficiency and output:
1. Automation
Automated systems minimize human intervention, ensuring consistent quality and efficiency throughout the production process. Features such as real-time monitoring and data analytics provide manufacturers with actionable insights.
2. Internet of Things (IoT)
IoT devices enable batching plants to connect to the internet for remote monitoring and management. Predictive maintenance and real-time alerts help in preventing downtime and ensuring operational efficiency.
3. 3D Printing Technologies
The integration of 3D printing with concrete technology opens new avenues for construction. Mixing equipment can adapt to produce specific concrete mixes that can be used directly in 3D printing applications.
Conclusion
A concrete batching plant is an invaluable asset in the construction industry. Its ability to produce high-quality concrete consistently and efficiently makes it a cornerstone of modern building practices. By understanding the functionality, benefits, and technological advancements in batching systems, construction businesses can elevate their project execution standards and remain competitive in an ever-evolving market.
For more information about state-of-the-art concrete batching plants and other construction equipment, visit Polygon Machinery.